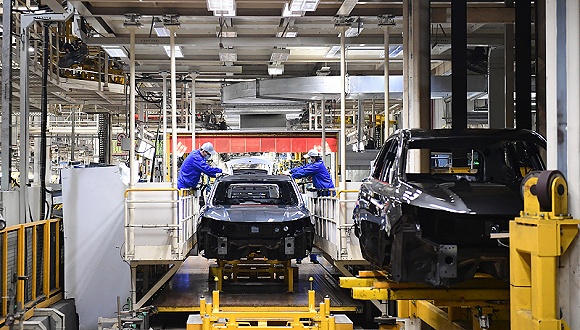
汽车公司信奉了数十年的精益生产模式似乎到了必须要重塑的危急关头。
过去两年,一颗成本5元不到的芯片成了汽车公司老板们高价求购都得不到的“期货”;一个随处可见的线束成为制约汽车生产下线的“绳索”。越来越多的人意识到,保住供应链才能保住企业的生命线。
从亨利·福特创立第一条汽车生产流水线,实现汽车大规模生产,到丰田英二打造精益生产模式,强调成本优先效率至上,汽车制造业百年间经历了两次里程碑式的革新。尤其后者强调的的上游零部件只够供应下一步立即需求的JIT准时生产系统(Just in Time),受到了广泛汽车公司的追捧,并且一直运行畅通。
但是,随着新冠疫情的开始,芯片危机、原材料价格疯涨以及局部地区冲突,高效紧绷的汽车供应链陷入极度不确定中。强调“抵御冲击”的韧性变得比成本和效率更加重要。以成本和效益为出发点的汽车工厂生命线是否已经到了再度变革时刻?
疫情凸显出了供应链韧性不足
3月以来,全国疫情呈现多发态势,长春和上海两大重要汽车生产基地影响严重。根据中国汽车工业协会的数据,4月份汽车产销环比和同比均遭到“腰斩”,供应链运单与去年同期相比也下降66%。
理想汽车和蔚来汽车4月份分别只交付了4167台和5074台车,在造车新势力企业里排名垫底。理想联合创始兼总裁沈亚楠称,理想汽车的零部件供应商超过80%分布在长三角地区,其中大部分位于上海、江苏昆山。“部分供应商无法供货,有些供应商甚至完全停工、停运,导致现有零部件库存消化后无法继续维持生产”;蔚来汽车创始人李斌解释,3月中旬开始就有零部件断货,只能靠着库存勉强支撑。
精益生产模式下运行的汽车工厂通常不会备大量库存。哪怕经历一次武汉疫情后,汽车公司已经拉长了安全库存,最多也只能维持一个月的生产。
相比新势力公司,传统汽车公司的零部件短缺情况更加严重。一家传统汽车制造公司的供应链管理人员向界面新闻透露,“现在已经没有个人生活,每天都在忙着捞人捞料。”
汽车制造商们受到的断供影响不单来自一级供应商,四五级的中小型供应商停产都可能触发连锁反应,导致整个生产系统失灵。
变速器巨头采埃孚的内部员工向界面新闻介绍,由于上游江苏太仓和昆山的供应商暂停生产,导致原材料短缺产能放空,“只能对客户延迟交付”。
另一家专做氢燃料电池的二级供应商表示,“上游线束供应商暂停生产后,库存只够用三天,用完后客户找我要货也没了。”为了能够保证供货,这家供应商专门找了小面包车运货,额外增加了许多物流成本。但为了防止客户流失,这是必须付出的代价。
传统汽车零部件的供应方式是以主机厂为中心,一级一级往下推导的纯链状式过程。汽车制造商为了缩短供货周期,减轻库存压力,会选择与供应商伙伴在生产基地周边建立配套工厂。长期下来,汽车工厂周围聚集起大批零部件厂商,并逐渐形成了庞大的汽车产业集群。
多名汽车分析师向界面新闻表示,此次行业普遍受到较大打击,一个关键原因在于疫情发生在上海及长三角这个国内最重要的汽车产业集群。
2021年,上海汽车产量达到283.32万辆,全国占比10.68%,相当于全国每生产10台车,就有一台来自上海。如此大规模的汽车产量得益于上汽集团和特斯拉上海工厂两大重要汽车制造商——前者以24%的市场占有率保持全国领先,后者去年的交付量达到了特斯拉全球交付量的一半以上。
以整车厂为核心,上海及长三角地区的零部件厂商星棋罗布。作为全国最大的汽车零配件生产基地,上海拥有华域汽车、科博达、动力新科等多家市值超百亿的上市汽车配件公司。并且,全球前十大零部件集团的中国总部有九家均位于上海,包括博世、采埃孚、法雷奥、大陆集团等。
以特斯拉为例,国内共有186家上市企业直接或间接为特斯拉供应零部件,其中,长三角供应商达到56%,供应链辐射周边600公里左右。
盖世汽车研究院总监王显斌告诉界面新闻,“正因为它对上海及周边地区供应链依赖大,受到的影响也最明显。”4月特斯拉在华销量仅为1512辆,环比下跌约98%。
在绵密的供应链传导下,密集布局该地区的诸多主流零部件企业对下游整车厂商的辐射范围远超长三角本地,遍及全国。
东风日产位于广州花都工厂的部分生产线就在4月份遭到停产危机,因为该工厂有83家核心零部件供应商都在上海。
往前两个月,总部在保定的长城汽车和在重庆的长安汽车销量分别下跌20.5%和15.1%,共同原因是头部汽车零部件厂商博世的苏州工厂出现疫情,车身电子稳定系统、安全气囊控制器等物资供应严重短缺,致使产量持续下滑,终端资源严重不足。
而汽车公司从2020年开始遭遇的芯片危机也折射出了现有供应链的诸多问题。张斌是国内一家大型传统汽车公司的采购经理,他向界面新闻透露,去年一颗芯片价格最高的时候炒到了2000多,还不一定能买到。
一些新势力汽车公司的老板已经在社交平台上直接发文求芯。小鹏汽车创始人何小鹏透露,有些人以上千元的价格提供成本仅个位数的芯片。
多名业内人士告诉界面新闻,博世、大陆集团等一级供应商现在拥有很高的议价权,它们为汽车公司提供总成设计,芯片采购也由它们统一调度,是不少汽车公司的独家供应商。
以博世L9369芯片为例,这是博世车身电子稳定系统(ESP)的核心芯片,供货给国内70%的汽车公司,去年在现货市场上一度炒到了6000元一颗。今年2月,长城汽车销量下跌20%的主要原因即博世ESP芯片供应不足,被扼住了生产的“喉咙”。
威马汽车CEO沈晖近日在社交平台发文证实,博世即将对一批必不可少的芯片涨价,智能电动车的芯片成本已经超过电池包。有电子电器采购经理直言,“要么接受价格,要么就不要芯片。”
疫情凸显了现有供应链韧性不足的问题,也让越来越多的汽车制造商意识到供应链模式必须改变。
供应链是否到了变革时刻?
多数业内人士给出的答案是汽车供应链需要被重塑,且正在经历这个过程。
汽车制造行业是一个资本密集型产业,前期需要投资数百亿元建厂、制造设计上万种独立零件并完成组装才能下线销售。精益生产最直接的目的是提升生产效率,实现成本最大化压缩。
在精益生产模式下,客户下单的订单数量反馈给工厂,工厂释放给供应商,再通过上下游协同,保证从供应商到工厂再到装配线的顺畅流动,实现“零库存”的最高目标。
需要被重塑和变革的并非精益生产模式本身,一个极具说服力的证明是作为精益生产代表的日企反而在这次芯片短缺危机中受到的影响相对较少。一方面是因为日系汽车公司智能化发展相对缓慢,更重要的是日系公司践行的精益生产模式更加细致与精密。
奥纬咨询董事合伙人张君毅在接受界面新闻采访时表示,汽车制造的关键是质量、成本和交付时间。当零部件短缺且物流紧张时,生产节奏就无法保证,生产成本相应增加,交付时间无法预测。
“汽车行业以前按月按周进行规划,但现在是按天甚至按小时供给。汽车公司的长期规划已经失效,只能随时变通。“张君毅说,“过去奉行的精益生产模式在这个极限状态下已经局部失灵且不可持续了。”
数字化服务提供商埃森哲大中华区产品制造事业部董事总经理蔡沈隽告诉界面新闻,精益生产并没有过时,只是制造商在践行这一模式时有很多局限性,投入的资金、人力以及管理系统都十分有限。“外部环境的不确定因素在增加,现有运作方式的空间被无限挤压,供应链的韧性和生产制造的成本控制都会面临较大挑战。”
麦肯锡全球董事合伙人方寅亮对界面新闻称,现行的精益生产模式需要进一步升级和演化。供应链模式必须改变的原因之一,是以汽车制造商为中心而构建的供应链格局已经被打破。汽车智能化发展使得传统机械架构正在向智能化架构转移。这种架构的转变带来了整个体系内话语权的转移,上游供应商的议价能力在提高,“供应商可能不再听从制造商所谓的精益生产要求。”
理想汽车供应链电子电器总监卢继平在一场探讨供应链韧性的论坛上表示,汽车的供应链庞大冗长,涉及企业数量极多。汽车制造商目前只能管理到一级以及二级供应商,对于如何管理更加上游的供货商是个相对长远的话题。
卢继平坦言,“比亚迪的产业链和供应链是垂直一体化的,所以它在疫情中受到影响较小。但新势力汽车公司目前还无法实现。”
作为一线工作者,张斌更能直接感受到汽车制造商与供应商之间的关系转变。他告诉界面新闻,传统汽车制造商习惯培养自己的供应商体系,但两者之间始终无法做到像日系企业那样与供应商深度绑定。现行的供应商体系中很大程度上借鉴了欧美汽车公司的经验,制造商与供应商存在微妙竞争,更多是一种双向选择。“原来是芯片厂求着一级供应商,主机厂不需要接待芯片厂的人。现在是主机厂去求着芯片厂。”
另一方面,汽车公司习惯了的精益生产模式已经不再适用于所有的零部件品类。方寅亮告诉界面新闻,特别是和电子电器架构相关的战略性物资品类,需要汽车公司更深入地参与上游的管理,与上游供应商一起重新搭建从研发到制造再到供应的新模式。“只有加强了对上游核心资源的掌控力度,汽车公司才能更好应对不确定性。”
方寅亮还指出,消费电子公司未来也可能会加入造车领域。这些公司拥有完整的供应体系,甚至会把在消费电子整套供应商接入到汽车行业内,这可能会颠覆现有的传统供应链体系。根据麦肯锡此前做过的统计,全球芯片消费总量中汽车行业仅占比10%,一些大型消费电子公司的单一芯片采购量就可能与整个汽车行业采购总量相同。
“汽车制造商需要对这样的场景进行更透彻的思考,才能够在供应格局发生变化时免遭降维打击,”方寅亮表示,“至少做到更好的前瞻管理和风险管控。”
此外,传统汽车公司在过去追求生产出多款车型来满足不同国家的出口需求,但现在意识到需求多样性带来的是无比脆弱的供应链。
以最常见的线束为例,传统汽车公司生产制造的一台汽车身上就有上百种线束,即使供应商足够多也会因为需求计划经常变化,导致供货不足。张斌透露,“为了不同需求,线束经常发生改动,有时备了货也用不了。”
这也造成了供应商的利益损失。他们常常面临订货数量和品种的突然变更,而且通知期非常短。因此,供应商预存制造好的零部件还不够,手边还要有很多原材料库存。
值得注意的是,小规模、可预测性低或预测前置时间短的风险实际上是高频率发生。麦肯锡研究发现,在过去35年里,平均每4.9年会发生一次对汽车产业链冲击持续时间超过2个月的突发事件,平均3.7年发生一次冲击持续时间1至2个月的突发事件,平均2年发生一次冲击持续时间1至2周的突发事件。
研究报告强调,全行业需逐步改变传统学院式、追求成本及效率最优的供应链策略,转而以增强供应链韧性为核心目标。
所有人都在寻找答案
尽管行业已经普遍认同以成本效益为出发点设计的现代供应链到了需要改变的时候,但具体调整的方向和改变幅度都还在摸索之中。
方寅亮认为,汽车制造商需要进一步优化与更新不同的零部件供应品类。传统物资的供应格局没有发生根本变化,产业体系也相对稳定,传统精益生产模式继续适用;其中涉及国际供应链的品类在继续推行精益生产的基础之上,需要更加快速动态地关注市场供需变化,以优化供应来源和调整库存水平;与电子电器和软件架构相关的品类则需要重塑供应格局,汽车制造商需要根据具体情况更深入地参与到上游包括研发、制造、物流领域的合作,重新构造供应模式。
“汽车制造商需要针对不同的品类去了解供需关系变化,”方寅亮说,“只有采取相应策略并进行合作与整合,才能形成具备韧性的供应模式。”

短期内放在首位的措施是加大库存储备。一家和上汽集团有合作的动力电池供应商向界面新闻表示,疫情期间公司行动较早,工厂将库容场地都腾出来储放风险物料。“至少备了一个月(库存),有的备了两个月。”
对于芯片这类高价值高敏感类零部件,汽车制造公司会提前半年下订单,最紧缺的时候甚至要提前一年,且订单数通常会高于实际需求量。据张斌透露,为了提高优先级序位,公司还会利用平台优势,主动找到芯片原厂中国区最高负责人或者到芯片原厂盯料,确保第一时间拿到货源。
但并不是所有品类零部件都适合扩大库存。卢继平认为一些大型零部件建库存会带来高昂的成本,更合适的方法是与供应商在生产基地周边建配套厂,将供应链辐射半径进一步缩小。
除了增加备货,企业还会选择开发B点供应商,分散风险。上述生产氢燃料电池的二级供应商正在考虑在上海以外的地方寻找备用零部件厂家。但这需要多家供应商之间密切合作,增加管理成本的同时也削弱了规模化效应。
“短期内可以不考虑成本这样做,但长期找不到平衡方案,公司只会倒闭。”该供应商无奈地表示,“库存增加到多少时可以规避风险,开发B点是否有意义,我们还在摸索,目前很难找到合理的方案。”
中小型供应商会倾向于保留精益生产模式,他们在面对危机时更脆弱,做出调整也更伤筋动骨。汽车公司会更迫切改变,哪怕没有疫情,供应链数字化管理也已经在推进。这是平衡成本与韧性的有效举措。
蔡沈隽告诉界面新闻,供应链应采取数字化管理能够帮助汽车制造商回归精益生产的本质——数据能够预测、可见、互相连接并且具备实时性。新势力汽车公司没有历史包袱,在供应链数字化方面表现最好。合资企业与国内传统汽车制造商基于过往经验,也开始纷纷采取相应行动。
数字化管理可以帮助汽车公司更为灵活地应对各种可能发生的变动,“以前和供应商协同,预计交货时间可能是一个月以后,现在通过数据赋能就可以知道这批货正处在哪个生产制造环节。”企业通过数字化手段模拟各种情境灵活调整供应链安排,从而提高供应链弹性。
这种精细化还体现在对上游供应商的管理上。和大部分选择增开备选供应商的企业不同,一些大型传统汽车公司正在考虑精简供应商数量,并与其达成更加深层的战略合作。
张斌认为,“需要提高供应商对主机厂的忠诚度。彼此成为利益共同体后,遭遇类似疫情的情况,供应商才愿意倾斜资源。”比如日系汽车制造商就与芯片厂商签订了长期合作协议,包括保供优先级的条款。
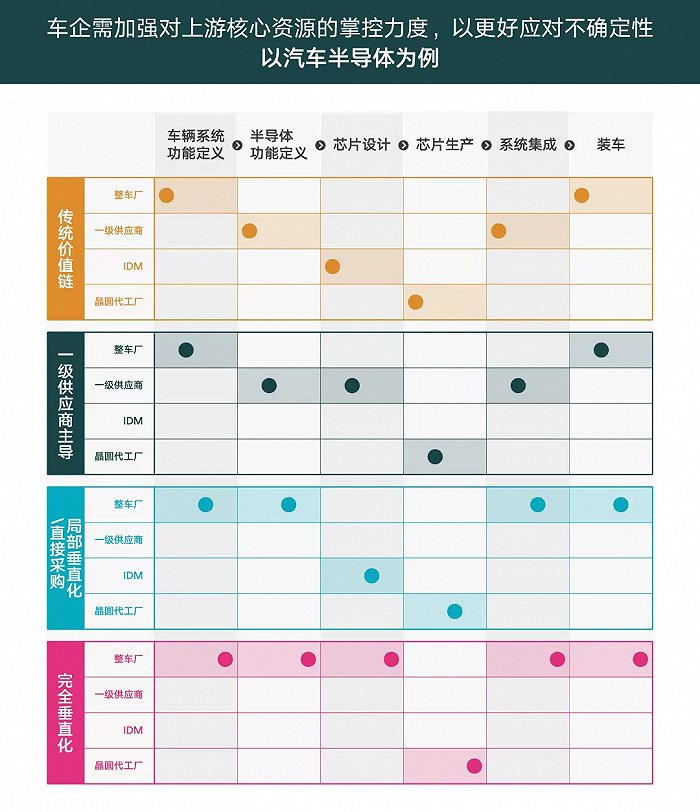
传统汽车公司也开始计划减少零部件种类,尽可能使用通用型零件,从源头控制供应商数量。特斯拉是一体化压铸车身技术的先锋,Model Y(配置|询价)后底板从70多个零部件减少至只有两个,节省了成本也缩短了供应链。
中信证券研报指出,国内的造车新势力以及海外大众、沃尔沃和奔驰等品牌纷纷跟进这一技术趋势,一体铸造已是大势所趋。根据测算,2030年全球范围内一体铸造的渗透率有望达到30%。
除了车身一体压铸技术,特斯拉还在尝试将电芯集成到底盘上(CTC)。这项技术加深了电池系统与电动车动力系统、底盘的集成,减少零部件数量,节省空间,提高结构效率。零跑汽车日前也已公布其CTC方案。
方寅亮认为,传统汽车行业已经走到非常成熟的阶段,必须从技术、流程和产品本身探索降本增效的突破口,让企业在变换大环境里维持供应链韧性。汽车公司也在通过自研减轻上游独家供应商带来的风险。
“以电池供应格局来说,每一家汽车公司都在尝试发展自己的电池供应系统,亲自参与零部件的研发设计和制造。”芯片同样如此,麦肯锡调研发现,68%的汽车公司倾向于参与或主导车辆系统功能定义和半导体功能定义,再由芯片公司负责设计和生产制造。
尽管面前还有很长一段路要走,但是汽车公司都在采取措施积极应对。从短期的应急举措,到中期的数字化管理,再到长期的供应链结构布局的转变,汽车公司已经深刻认识到,现有的精益生产模式不是一成不变的灵丹妙药,它必须和时代共同发展。
(应采访对象要求,张斌为化名)