进入2021年,电气化已经成为汽车行业的大势所趋。主机厂正积极在全球布局纯电或者混合动力汽车,零部件供应商纷纷推出最新的“三电”等新能源汽车核心零部件产品。作为汽车行业上游供应商,如何应势而行并满足客户日益增长的需求?这对材料供应商来说,既是挑战,也蕴含机遇。
随着碳排放的政策日益严苛,全球已有多国将禁售燃油车提上日程。日本政府考虑从2035年起,停止销售纯内燃机车辆,在售新车必须是纯电动或者混合动力汽车;英国则更为激进,将禁纯燃油车的时间表从2040年提前至2030年,截至2035年,混动汽车也将停止销售;聚焦中国,去年颁布的《节能与新能源汽车技术路线图2.0》指出,到2035年,我国汽车产业要实现电动化转型,传统能源动力乘用车全部为混合动力,新能源汽车成为主流。
受此影响,全球主机厂和零部件供应商分别加快新能源汽车相关核心部件的布局,汽车行业的电气化正在全速推进。由于新能源汽车对轻量化、安全性的需求更为迫切,材料供应商相比内燃机时代面临更严峻的挑战。
作为全球领先的高性能材料提供商,杜邦一直致力于不断创新并研发适用于新能源汽车领域的产品和应用。在提升整车性能和用户体验的同时,帮助整车厂商减碳降耗。
近期,本刊记者采访了杜邦交通与材料事业部全球副总裁兼亚太区总裁、先进解决方案总经理吴桐。我们一起来聆听她如何讲述在全球电气化浪潮下,杜邦如何以创新的解决方案来应对行业挑战。
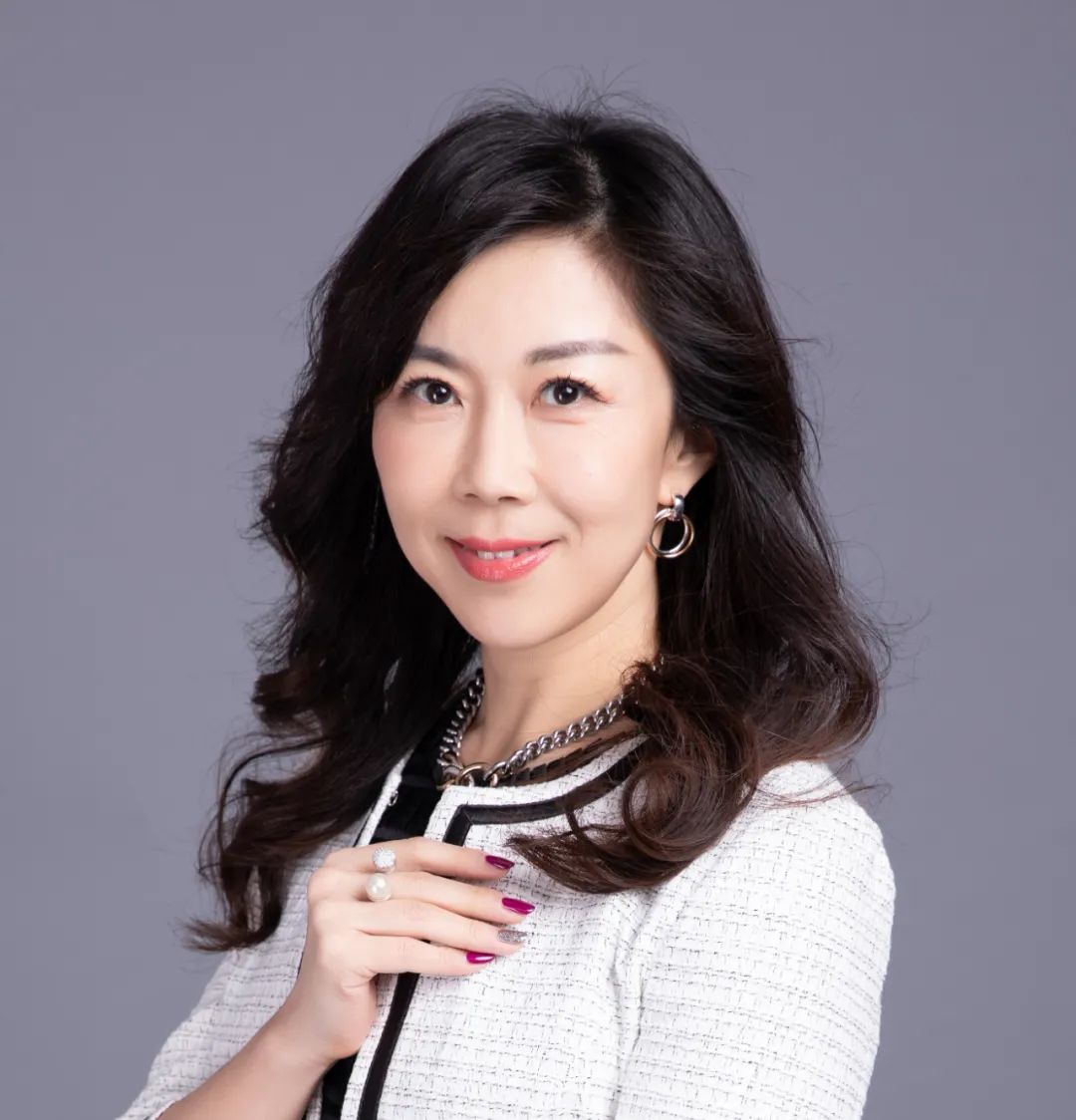
杜邦交通与材料事业部全球副总裁兼亚太区总裁、
先进解决方案总经理 吴桐
电气化下的挑战和机遇
随着环保政策在世界各地的迅速落地,主机厂不断地提高新能源汽车在自家产品组合中的比例。以2025年为时间节点,大众计划将新能源汽车销售比例增加到25%,丰田则将完全至少搭载混合动力系统,而通用将在2035年实现全面电动化。
电气化给新能源车市场带来飞速的增长,材料供应商也面临更多的市场机遇和挑战。在电气化的趋势下,大部分汽车部件都要求将轻量化做到极致,并且安全标准更高。由于增加了电机电控和电池的三电系统,材料在实现高性能、高效率的同时,可靠性稳定性要求也上升到新的台阶。比如无卤阻燃、电磁屏蔽、高相对漏电起痕指数(CTI)、导热以及高压电力系统的阻燃产品等。
以动力电池而言,五年前刚推向市场的纯电动汽车续航普遍还在300公里以下,而短短几年间,续航里程达到450公里以上的车型比比皆是,甚至1000公里续航的电动汽车已经纳入了讨论范围。动力电池性能若想实现革命性的突破,高性能材料将在其中将发挥不容忽视的作用。杜邦在这一领域依靠新材料研发的实力,不断推出电气化解决方案组合,帮助汽车行业应对当前和未来的复杂挑战。通过开发可持续的先进材料方案,提高车辆的续航里程、安全性、热管理、耐久性、声学和整体性能。
“在这个快速发展的时代,每个客户的方案和蓝图都是不一样的。”吴桐还强调,“杜邦的优势是在设计阶段与客户深度探讨,利用我们长期在汽车行业积累的专业知识和创新材料的能力共同设计开发适合客户需求的解决方案,从而在最大程度上创造价值。”吴桐告诉记者。
新能源车动力系统—轻量化、更高效、更安全
对于新能源汽车的动力系统来说,轻量化、高可靠性、高效率的材料至关重要,有效提升航里程和保障车辆安全,这也是主机厂非常核心的痛点。
为提升轻量化,杜邦开发了BETAMATE™结构胶,为钢、铝、镁和复合材料等汽车基材提供高性能粘接。它取代了焊接和机械紧固件,减少了传统工艺中常见的疲劳和失效,大大提高了生产效率。同时有助于轻量化车身结构和电池组件,并且在不损失机械性能的前提下,减少焊缝并降低成本。
为了减轻汽车重量,从而满足日益严格的碳排放法规,多元复合材料在新车设计中的应用将越来越普遍。BETAMATE™结构胶有助于大幅降低二氧化碳排放量并减轻汽车重量。自1999年以来,共有超过70亿米的BETAMATE™用于汽车,这相当于减少了2300万吨二氧化碳排放并节省了26亿加仑汽油。
在安全性方面,电动汽车传动系统的安全性要求所用在高压环境中必须确保可靠,并且长期耐用。杜邦Zytel®和Crastin®两款材料能够同时提供高性能和安全性,是新能源汽车高压端子和连接器、母线、高压开关和继电器的理想选择。此外,Zytel®和Crastin®也可用于复杂的传感器系统和电子元件,如开关、连接器和ECU(电子控制单元)。这两个产品系列是专门为提高组件的耐用性而设计的,在不同的温度级别下,可以获得更好的安全性、效率和连接性能。
新能源车热管理—防止热失控、优化成本
即使新能源车动力电池的性能发展迅速,续航里程越来越高,但是低温趴窝的问题仍然存在。在极端温度下,动力电池的性能表现通常差强人意,续航里程面临大幅缩短,这对推进电动化十分不利。因此,新能源汽车的热管理系统逐渐受到重视。
杜邦BETATECH™热界面材料有助于车辆在充电和运行期间保持最佳的电池温度,从而延长车辆行驶里程,并由于减少了热失控的可能性而提升车辆的安全性。用于电池包组装的BETAFORCE™TC导热2K粘合剂可用于将主动冷却单元粘到电池电池或模块上,使电池包减重30公斤。这些粘合剂还可以显著减少所需组件的数量,优化电池包设计的成本。此外,BETAFORCE™TC可以实现快速涂覆并能支持大批量生产。
另一方面,目前行业的主流趋势是将电机、电控和减速器集成为“三合一”的设计,冷却介质从50%乙二醇切换到新型变速器油,这就对相关的塑料零部件提出了长时间耐变速器油老化的要求。杜邦正在加强这方面的老化数据积累,以应对来自不同客户不同变速器油的老化要求。
电气化趋势下,杜邦积极开展战略布局
全球电气化浪潮袭来,在谈到这一趋势下杜邦的变化时,吴桐表示,“电气化时代,最大的变化就是,由于新能源技术不断在更新,因此需要材料供应商需要更快的响应速度来灵活应对市场变化。”
中国市场新能源汽车渗透非常迅速,杜邦十分重视中国本地化进程。杜邦在张家港粘合剂工厂已于今年11月破土动工,专门针对电动汽车轻量化的需求,新工厂将提供最先进的工艺能力和质量标准。
放眼全球,杜邦正在组建全球汽车电气化卓越中心(COE),重点布局三大关键领域,配备专门的人员和设备,以加速新技术的推广及应用:
电池安全技术中心(上海和日内瓦):目标放在提高动力电池能量密度、快速充电能力和成本优化的同时,帮助满足安全要求。
热管理技术中心(瑞士日内瓦和弗赖恩巴赫):目标是在成本可控的情况下,帮助提高快速充电速度和在寒冷天气下的性能表现,同时保持电池的可靠性。
e-动力总成效率技术中心(日内瓦):目标是提高电力电子和电机效率和能量/包装密度,同时保持最佳可靠性。
下一步,杜邦将与更多新进入电动化市场的企业合作,“近年来最大的变化是,我们与很多造车新势力建立了合作伙伴关系,我们通过提供优异的材料解决方案,帮助他们在三电系统以及电力电子方面实现创新,杜邦希望和客户共同努力,为行业提供最创新、最可靠的解决方案。”