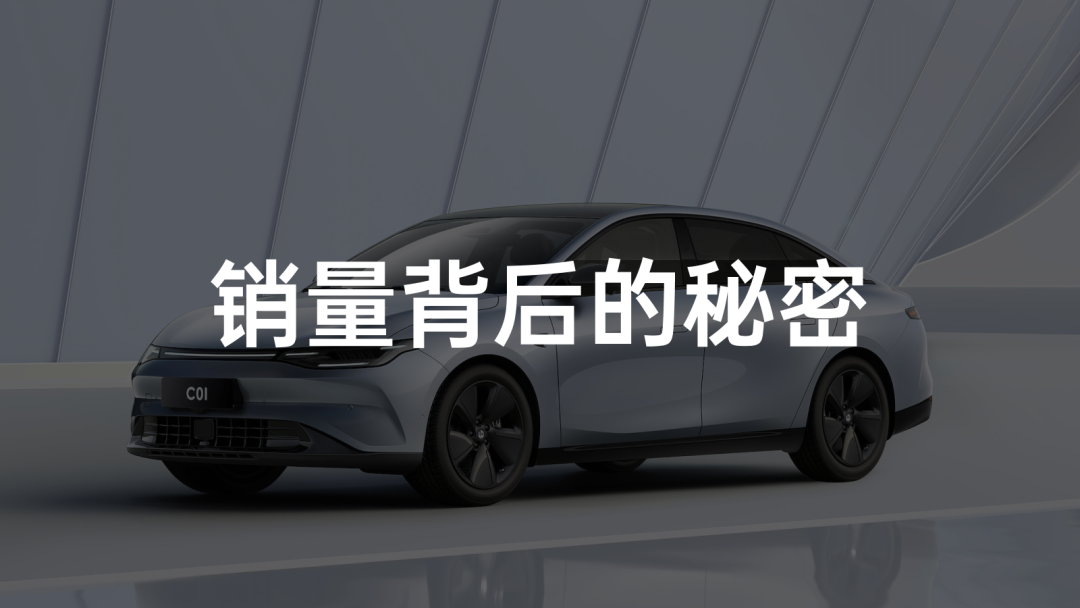
2022 的春天,就这样夹杂着惆怅与不甘,在疫情之中悄悄溜走了。
但是一个人的时光或许会虚度,一个行业的发展却一定是时不我待的,尤其是在竞争越来越激烈的新能源汽车领域。
前几日各家新势力发布了 5 月份交付量成绩,各自悲喜按下不表,我从中发现了一家非常有意思的品牌——零跑。
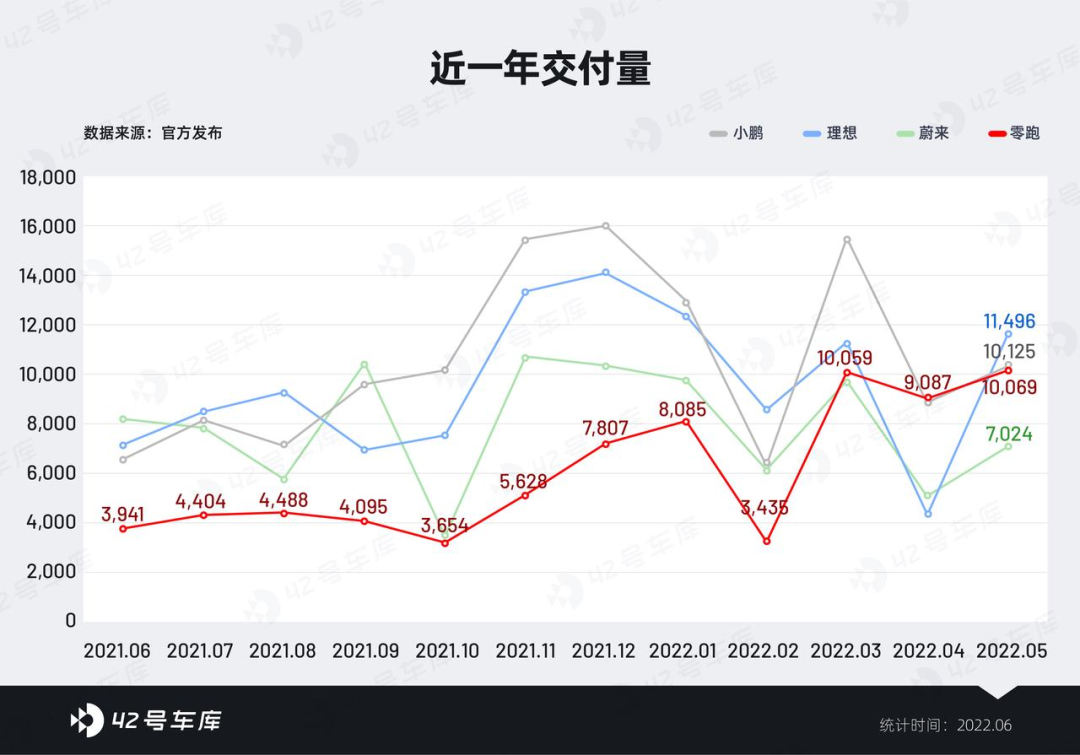
这家以性价比著称的新势力,不但在不觉间跻身于第一梯队,而且还在新车新技术上赚了不少风头,尤其是最近大火的国内首家量产 CTC 。
那么,今天咱们就来仔细地盘一盘零跑和它的 CTC 技术。
为什么说零跑有意思?
在一年以前,大概除了汽车行业从业者和车主之外,可能很少有人听说过零跑这个品牌。而自去年底 C11(配置|询价) 正式交付以来,交付量便以黑马姿态一路上扬,在严重的产能限制之下,都已经来到了新势力的第一梯队,尤其是在疫情艰难的 4 月,不得不令人刮目相看。
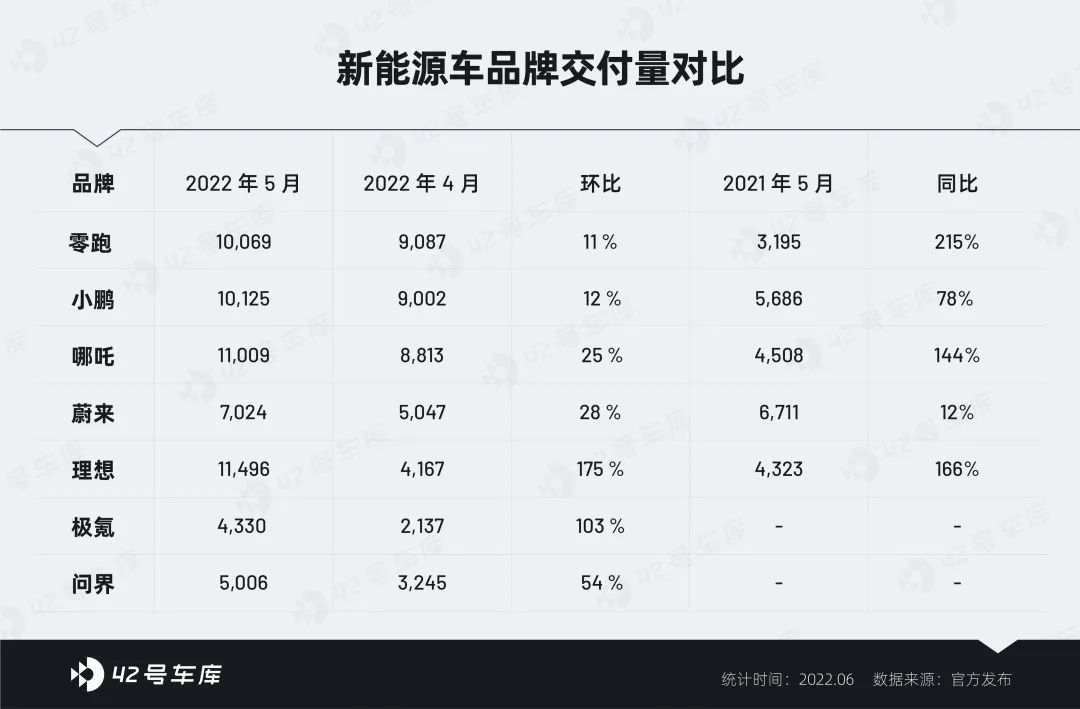
在 4 月底发布,并于近期登陆粤港澳车展的 C01 更是继续了零跑的爆款气质。5 月 10 日开启预售,4 小时订单量就超过了 2 万台;预售 48 小时,订单量破 3 万台;到 5 月 28 日,零跑科技副总裁曹力在粤港澳大湾区车展上表示 C01 订单已突破 45,000 台。
如果只把这些成绩归功于性价比,怕是过于肤浅。性价比当然是销量快速攀升的原因,但如何实现性价比,即如何控制成本的前提下提供超越用户期待的产品力,这才是更值得分析研究的。
零跑的创始人朱江明在 4 月底 C01 和 CTC 的发布会上淡淡地说了这样一句话:
“「除了电芯,全是自研」。”
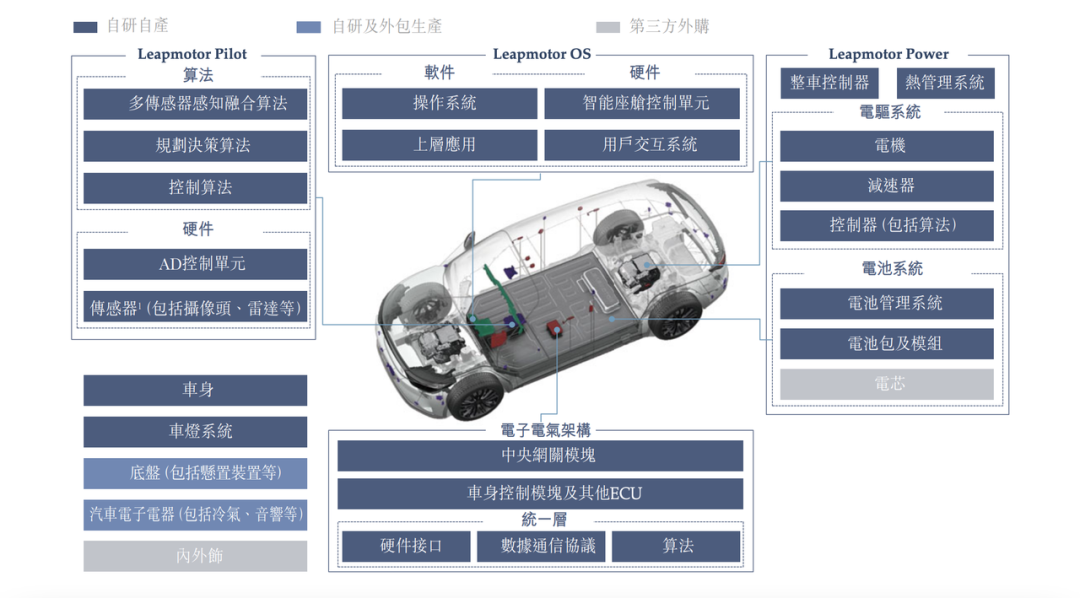
更确切的说,零跑除了内饰和电芯,全是自研。据 3 月份的零跑港股招股书,其研发范围覆盖了 Leapmotor Pilot、Leapmotor OS、Leapmotor Power、电子电气架构、车身和车灯等大多数领域。除了电芯和内饰不做以外,底盘(含悬架系统)、电子电器部件都要和供应商一同开发。
在传统主机厂,自研车灯的都少,但零跑甚至做到了自产车灯,初闻着实惊了一把。
正是在这样的自研信仰之下,零跑不仅实现了销量的快速发展,也推出了相当前沿的技术——国内首家可量产的 CTC 技术,这也就是咱们接下来要聊的主角。
CTC 和 CTB 是怎么来的 ?
除了 CTC,最近火起来的还有另一个词「CTB」。在分析它们是什么之前,必须先回答一个前置问题,它们的出现是为了什么?
这需要从电池包的历史谈起,因为在 CTC 和 CTB 之前,还有 CTP 和 CTM。
里程焦虑是曾经制约新能源汽车市场化的一个核心因素。为了增加续航,在动力电池层面的思路,就是让电池「装下」更多的电能。分解下去就是电芯材料和工程结构两个方面。好的电芯相当于内功,如何打造一身好筋骨来承受更多的内功,即如何在有限的空间内安排更多电芯,就十分考验电池包设计的工程能力了。
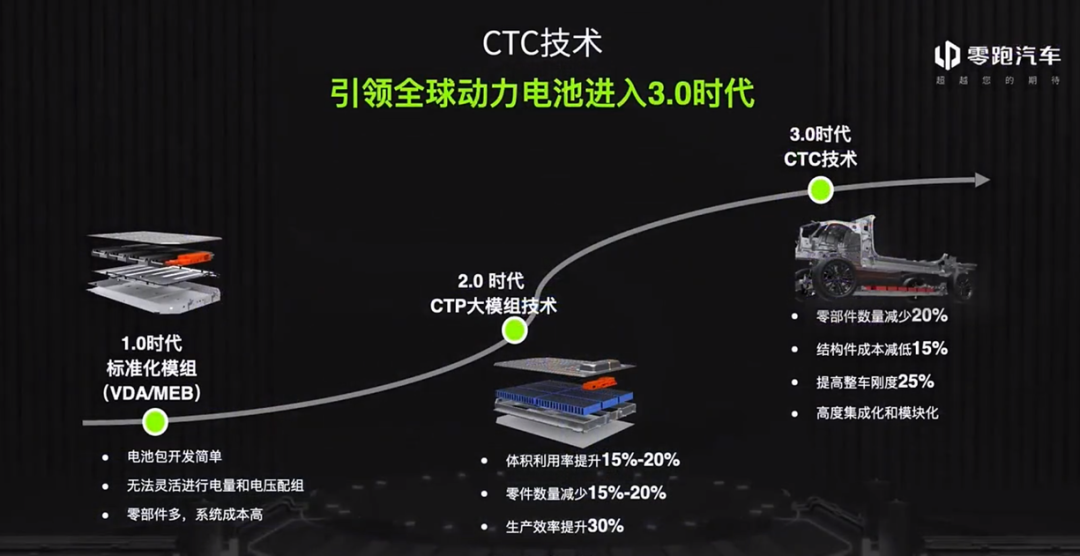
电动汽车发展早期的电池包形式,也是目前主流电动车采用的形式,就是标准化模组电池包(CTM)。简单理解就像是把大象装入冰箱的 3 步:
先把电芯组装成模组;
再把若干模组组装在一起加上外壳,成为电池包;
最后把电池包装在车身上。
模组的存在使得电池包在整体技术要求和装配方面变得简单,其明显缺点就是模组和外壳体积占用较多,空间利用率不高。于是便发展出了 CTP(Cell To Pack)技术,也称为无模组技术,即电芯直接集成到电池包内,减少或省去了电池模组,把电池包集成到车身地板上作为整车结构件的一部分。
CTP 的优势是提高了体积利用率,减少了零件数量,提高了生产效率。目前的行业发展水平正处于从标准模组向 CTP 技术转向的过程之中。而缺点则是碰撞安全、热管理和售后维护。目前采用 CTP 技术的代表企业有比亚迪、蜂巢新能源和宁德时代。
CTC(Cell To Chassis)技术则是指将电池、底盘和下车身进行集成设计,进一步简化产品设计和生产工艺的技术。通过减少冗余的结构设计,有效减少零部件数量,在提升空间利用率和系统比能的同时,车身与电池结构互补,使电池抗冲击能力及车身扭转刚度得到大幅度提升。
第一个让 CTC 火起来的推手是特斯拉。早在 2020 年 9 月的电池日(Battery Day)上,特斯拉发布了自己的 CTC 理念,并于今年 4 月真正实现量产,首搭车型是得州工厂的 Model Y(配置|询价)。
当时马斯克做了一个非常形象的飞机油箱比喻。以前是在机翼放一个油箱,而现在则直接让机翼结构本身成为油箱,因为「没有必要在盒子里再装一个盒子」。而 CTC 同理,核心就在于省去原来的「油箱」——电池包外壳。
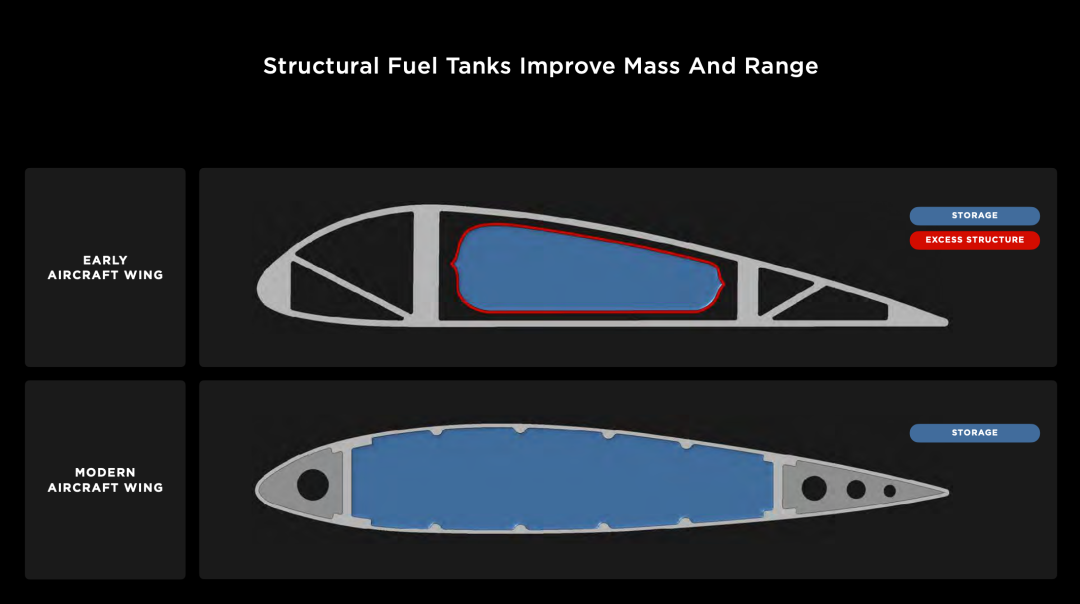
4 月底,高举高打「自研」标签的零跑发布了国内首家可实现量产 CTC 技术,首搭车型 C01,并放出豪言要将 CTC 技术免费开放共享,让 CTC 的概念再一次热闹起来。
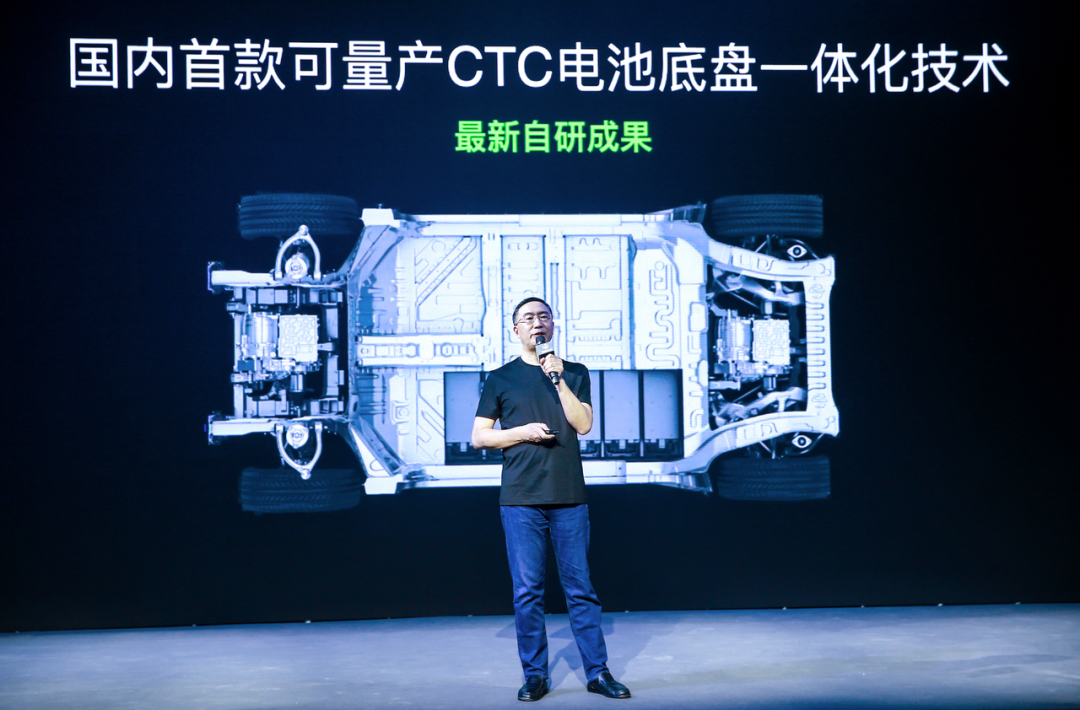
之后则是近期比亚迪在海豹发布会上一同发布的 CTB (Cell To Body)技术。CTB 与 CTC 有很多相似之处,都是强调电池、底盘和车身的集成化设计,代表了未来的技术方向,行业内已形成共识。大众、沃尔沃和宁德时代等都已在积极布局相关技术。
但是,到目前为止,达到量产水平的 CTC/CTB ,只有特斯拉、零跑和比亚迪三家。
详解 CTC 和 CTB
早期电池包设计上偏向于保守,一来是出于安全考虑,二来是技术实现上相对容易。从 CTM 到 CTP 再到 CTC/CTB,工程结构方面的进步是伴随着越来越成熟的电芯技术演化而来的,一切优化都是在确保电池安全的情况下演进的。
电池、底盘和车身一体化设计,高度依赖于车身底盘研发。与 CTM 标准模组和 CTP 相比,更需要整车企业的研发能力,在电池包设计方面需要更多介入,需要更全面的技术能力。或者说,敢先吃这螃蟹的,都是实力派。
具体的技术细节上,特斯拉的 CTC 是和车身一体压铸技术配合的,整车制造更加集成化。单纯看电池集成方式,特斯拉的 CTC 和比亚迪的 CTB 很相似,可以简单理解为上下两层面板中间夹了电芯,三者形成的电池包整体直接作为车身地板,省去了传统车身上的地板。
主要区别在于特斯拉的采用 CTC 技术的车身没有横梁,电池包本身就是承受载荷的结构件,做了特殊的结构加强;而比亚迪的 CTB 车身上则保留有横向钢梁,电池包不是主要受力构件。
特斯拉电池日展示
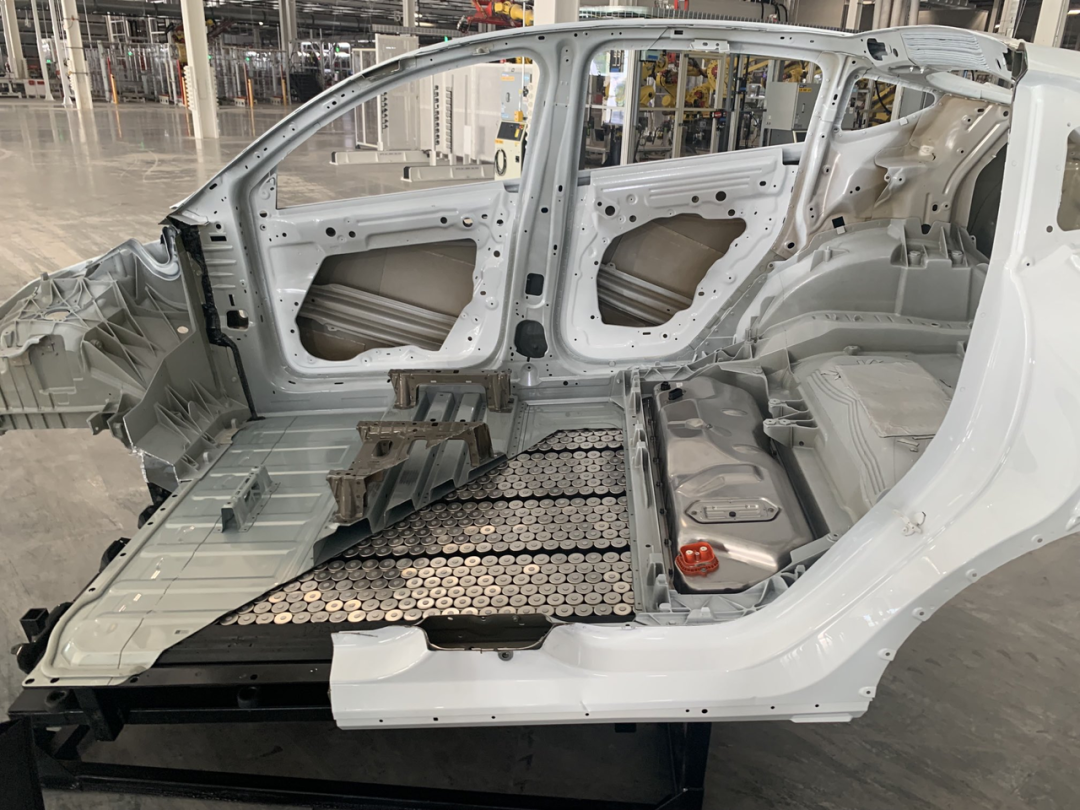
特斯拉 Model Y 的结构化电池
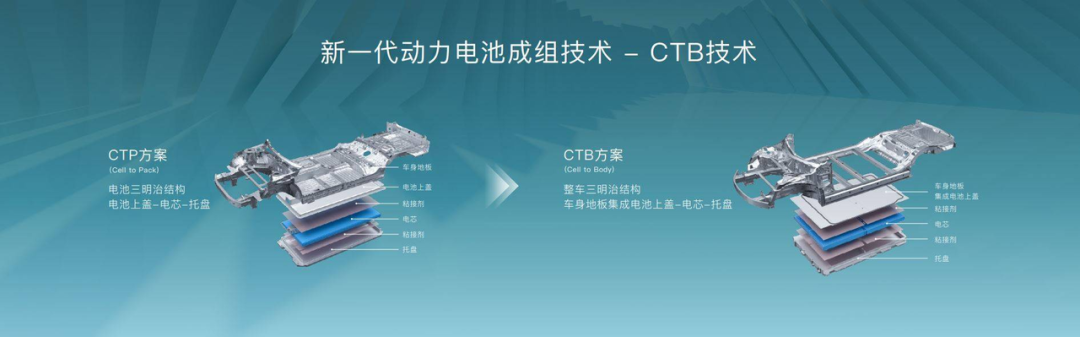
比亚迪 CTP 与 CTB 示意图
而零跑的 CTC 则是保留了原车身地板,在托盘上布置电池,再将托盘固定到车身上,以托盘、车身地板和下车体的横纵梁来封闭电芯。整个下车体底盘结构与电池托盘结构耦合,形成密闭空间,结构上更加紧凑,集成度更高。
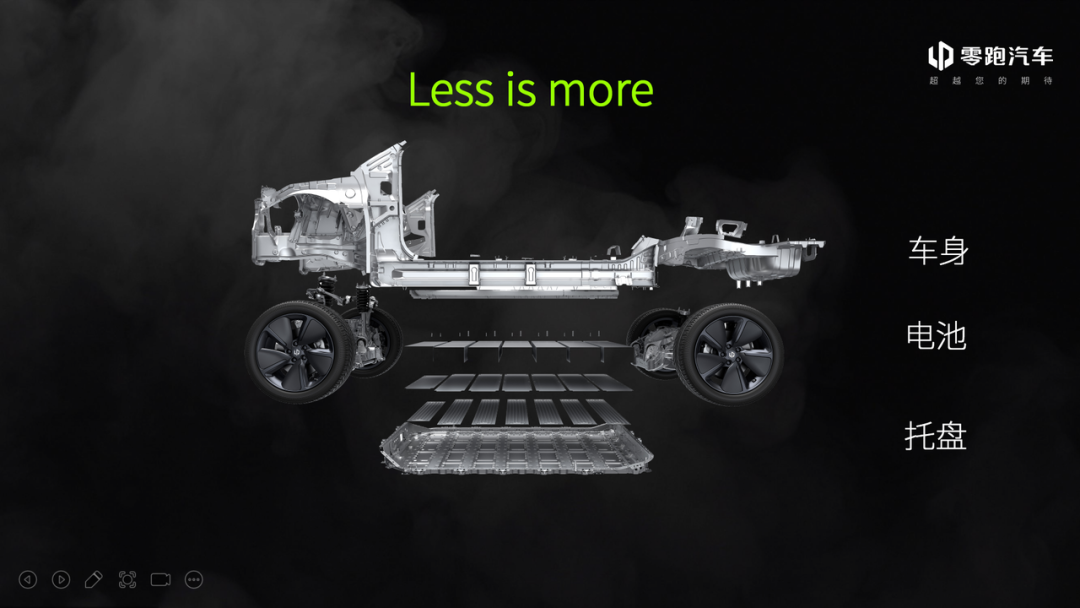
聚焦到零跑 CTC 和比亚迪 CTB 上,从结构设计来看,CTB 技术把车身地板面板与电池包上壳体合二为一, 与门槛及前后横梁形成平整密封面,通过密封胶密封乘员舱,底部通过安装点与车身组装。即电池系统作为一个整体与车身集成,电池包本身就是一个密闭主体。
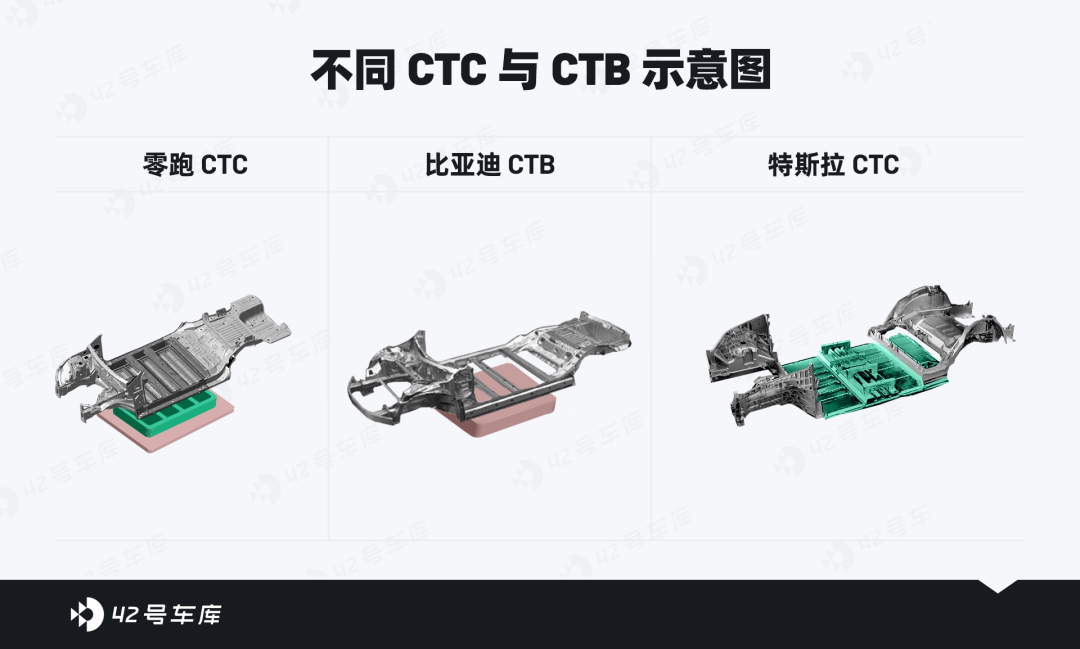
而零跑的 CTC 技术是借用了车辆底盘的基本结构,以车身结构梁与电池托盘形成双骨架环形梁式结构,通过车身设计与电池托盘形成一个封闭腔体,就像鸡蛋的外壳一样,整体扭转强度更好,整车集成度更高。
零跑这个把车身地板作为电池包上盖的设计,成为了全球第一个没有独立电池包结构的 CTC。

评价 CTC 与 CTB 技术涉及成本、电池装配工艺、电池密封、整车布置、车身刚度以及可维修性等等诸多方面,不存在绝对的优劣之分。每家的选择都是结合各自制造特长和产品特点选择的最优路径。
从电池方面讲,零跑 CTC 真正意义上取消了独立电池包,在电芯密封性上对制造工艺要求更高。与其他两位行业龙头相比,新势力中都算后发的零跑在技术上做到了 CTC 领跑者,相当难得。
特别是在电池的可维修性方面,与 CTC 的 Model Y 及 CTB 的海豹相比,C01 只需要拆解底盘上的电池托盘,完全与乘客舱隔绝,不涉及地板和座椅拆装,最为便捷。
零跑 C01 在 CTC 技术的加持之下,整体电池布置空间提升了 14.5%,垂直空间增加了 10 mm,这对于纯电轿车有限的头部空间来说,十分宝贵。车身扭转刚度提升 25%,有效提高了行驶性能、操控响应以及 NVH 表现。
也正是因为有了多项类似 CTC 这样的先进自研技术傍身,C01 以超过 5 m 车长的 C 级车身份,做到了 3 秒级加速,CLTC 续航 700+ km 的出色成绩,热销只是水到渠成。
写在最后
如果说 2010 年代是中国自主品牌汽车飞速发展的时代,那 2020 年代一定是自主新能源车井喷爆发的年代。
在过去的几年之中,各家新势力各领风骚,获得的关注度远远超过传统的合资强势品牌。如果拿学生上课打比方,那蔚小理和特斯拉肯定是坐在前排,表现最活跃的。
但是零跑这位同学就很有趣,低调腼腆,平易近人,最开始坐在教室后排默默无闻。遇到难题,当别的学生请家教找外援时,他自己在默默钻研。寒来暑往,一个个学期过后,零跑同学各科知识掌握得都很全面,不仅月考成绩已经名列班级前茅,而且提前自学了高年级课程,还乐于给其他同学讲解分享。
没有人会不喜欢和这样低调朴实又有实力的同学打交道。
品牌向上的道路是艰难的。零跑通过对自研的坚持,从 S01 起步,到 T03 稳住基本盘,再到 C11 学会了奔跑。等到了 C01 ,已经可以拿出 CTC 这样的先进技术了,这条艰难但正确的成长之路就这样被零跑走通了。
零跑对自研的信仰,有点儿意思。